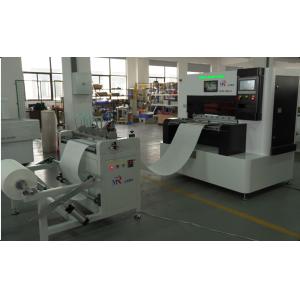
Add to Cart
800 mm Width Filter Paper Knife Pleating Machine
Max Width |
800mm |
Pleating Height Range |
3-60 mm |
Product Speed: |
380pleasts/min |
Power Supply: |
380V/60HZ |
Main Power |
10kw |
Working Air Pressure |
0.6Mpa |
M/C Weight |
580kg |
Features:
1. Filter Paper Knife Pleating Machine is automatic control of with CNC system.
2. Perfect design and reliable components ensure the high quality and excellent performance.
3. Filter Paper Knife Pleating Machine is steady that can ensure the high quality of the produced filter.
4. Touch screen operation. It’s very easy and friendly for operator.
Applications:
1.Filter Paper Knife Pleating Machine adopts upper and lower knife alternatively perform folding, from the knife automatic adjustment by computer, can reach different fold higher requirements, accurate size.
2.Filter Paper Knife Pleating Machine automatic dotting counter, folding processing and preheating and forming etc.
3.Filter Paper Knife Pleating Machine can also be folded all the different rules of fold change.
4.Filter Paper Knife Pleating Machine can change any angle,ensure the folding does not damage any kind of filter material.
5.This production line is suitable for the automobile industry three, hydraulic industry, purification industry, the water treatment industry.
FAQ
What are the specific functions of the CNC control system in the Filter Paper Knife Pleating Machine 800mm Width?
1.Precise motion control: It accurately controls the movement of the knife - pleating mechanism in the X, Y, and Z axes. For example, it precisely controls the lateral movement of the knife along the 800 - mm width of the filter paper (X - axis), the forward - backward movement during the pleating process (Y - axis), and the up - down movement of the knife for cutting and pleating (Z - axis), ensuring that the knife moves according to the set path and position to achieve high - precision pleating.
2.Pleating parameter setting: It allows operators to set various pleating parameters, including pleat height, pleat width, pleat pitch, and the number of pleats. Different product requirements can be met by adjusting these parameters. For example, for a filter requiring a higher filtration efficiency, the pleat height and width can be set appropriately to increase the filtration area.
3.Material adaptation: It can adjust the pleating process according to different filter paper materials. For instance, when dealing with thicker or more rigid filter paper, the system can increase the cutting force and slow down the cutting speed to ensure a smooth pleating process without damaging the material. Conversely, for thinner and more flexible filter paper, the speed can be adjusted accordingly to improve production efficiency.
4.Production monitoring: It monitors the running status of the equipment in real - time, including the speed of the knife, the position of the filter paper, and the operating status of each component. If any abnormal situation occurs, such as a knife jam or a motor failure, the system will immediately issue an alarm and stop the machine to prevent further damage and ensure production safety.
5.Data recording and analysis: It records production data such as the number of pleated filter papers, production time, and parameter settings. This data can be analyzed to optimize the production process, improve production efficiency, and detect potential problems. For example, by analyzing the data, it is possible to find out whether there is a trend of increasing knife wear, so as to arrange maintenance and replacement in a timely manner.
6.Programmable logic control: It realizes the logic control of the entire pleating process through a pre - written program. It coordinates the actions of various components, such as controlling the feeding mechanism to supply the filter paper at the right time, and ensuring the synchronization between the knife - pleating mechanism and the feeding mechanism to achieve a continuous and efficient production process.
7.User - friendly interface: It is equipped with a human - machine interface (HMI), usually a touch - screen display, which is easy to operate. Operators can easily set parameters, view production status, and operate the machine through the HMI without requiring professional programming knowledge, reducing the difficulty of operation and improving work efficiency.